Oyster Cultivation Environment
Project Background
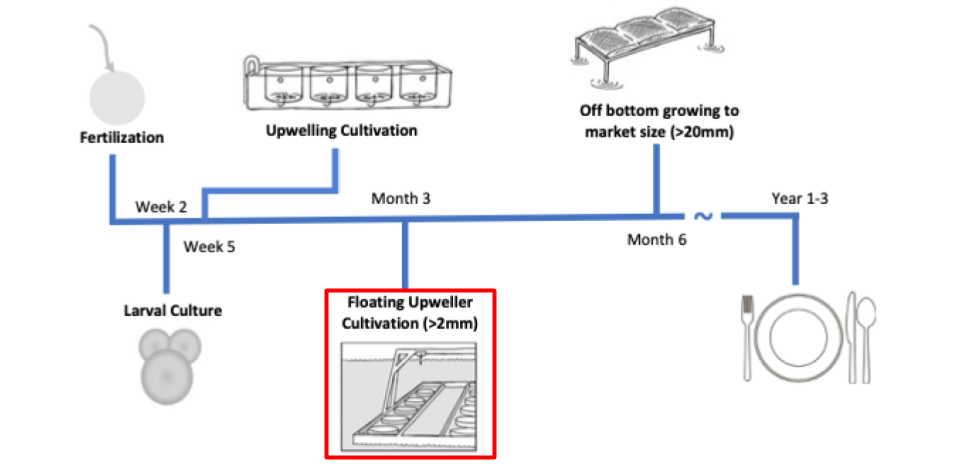
Oysters are grown in various environments throughout the duration of their lives, up until they arrive on your plate ready to eat. Hoopers Island Oyster Co., located in Cambridge, MD, manufactures this equipment to grow oysters from seed to shuck. One of these is a Floating Upweller System (FLUPSY), which grows oysters once they are roughly 2mm in size [1].
The basic design is an 8’ by 20’ deck with two plastic floats, a center trough, and eight silo & basket combinations. Mesh sizes are chosen according to the oyster seed the customer wishes to grow. Doors on the baskets protect them from the sun and provide for easier maneuverability around the FLUPSY. The baskets need to be removed every other day to clean the oyster seed and a seed shaker sorter is used once a week to sort the seed.
The oysters are placed in a basket with a mesh bottom, eight of which are placed in a floating platform. A sump pump is placed in a central trough and constantly pumps water out of the system, creating a slight height difference (Δh) between sea level and the basket water level. In turn, fresh ocean water is continuously upwelled through the bottom of the baskets, which provides oysters with a constant food supply of oxygen, algae, and phytoplankton.
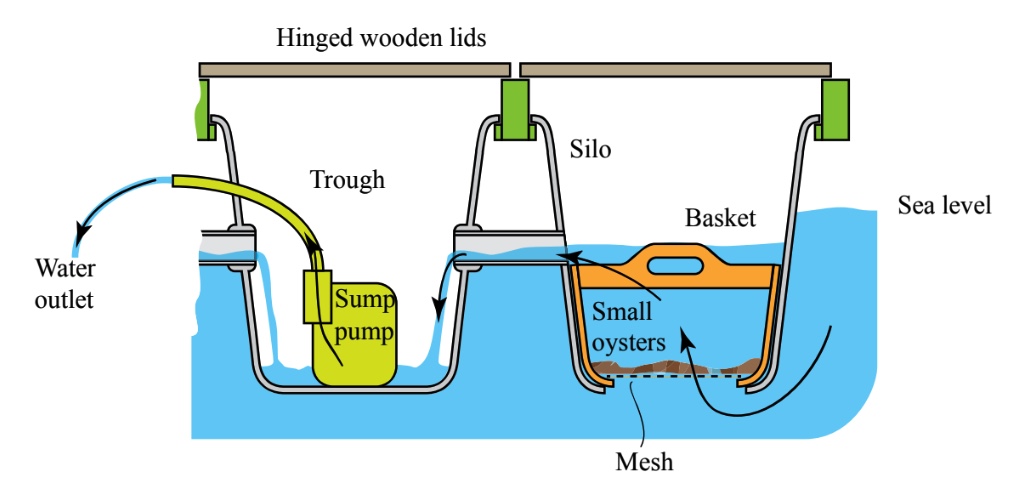

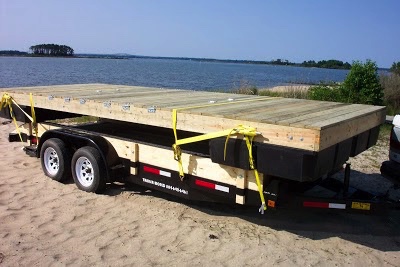
Young oysters thrive in the FLUPSY environment (~1mm of growth per week), as it provides a constant supply of food. It is proven to be affordable to end users and tough enough to survive for ten years in the water and sun without much maintenance. However, there are several areas of improvement:
- Manufacturing the components with fiberglass layups takes a lot of time, and is arguably more expensive than is required.
- The current 8' x 20' design (left) has difficulty shipping, which drives up the overall cost.
- Buoyancy is provided by rotomolded polypropylene float tanks, which is arguably more expensive than they need to be and takes up what can be considered wasted space.
- The central trough also has a large footprint for the simple task is does of creating a place for water to flow into and of housing a pump to remove the water.
- Although the FLUPSY has been proven to work, it still requires roughly 15 hours of labor per week to clean and sort the oysters.
Solution
We investigated two means of addressing the concerns above: (1) a thermoformed, modular floating upweller system and (2) a new method of growing oysters in a tumbling environment.
Modular Floating Upweller System
This is a modular design that allows the customer to choose the size of the system. Modules are connected to each other through a pipe network, and individual modules are preassembled when sent to the customer.
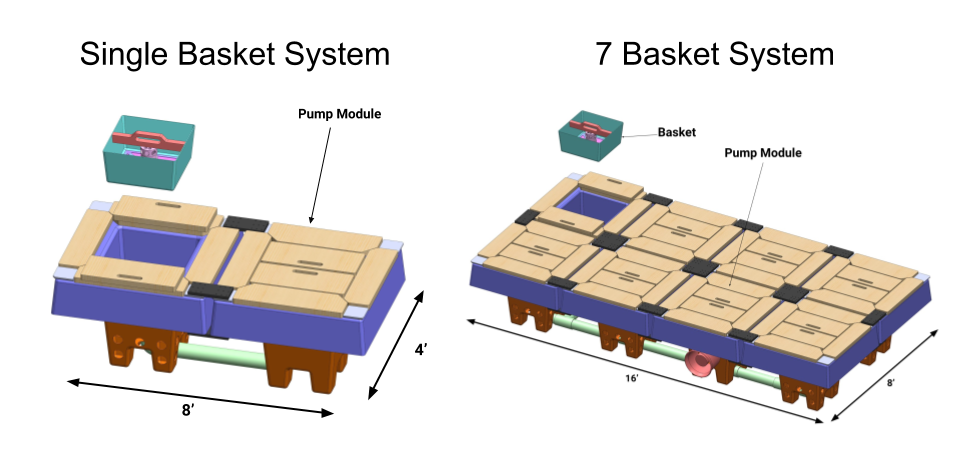
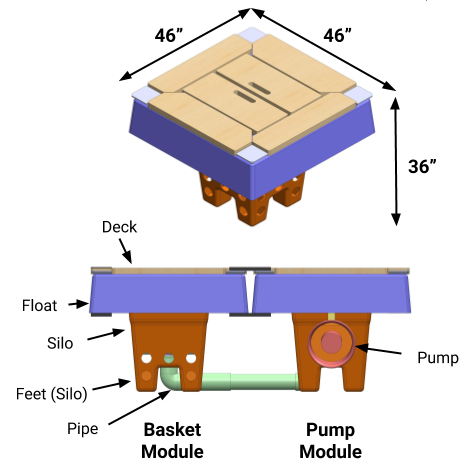
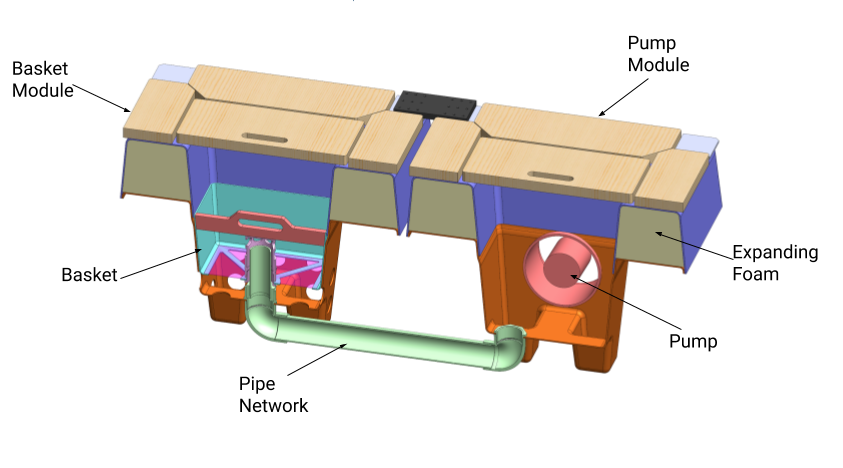
Modules have the same basic components, and are all connected by means of a 4” PVC pipe network:
- Wooden top deck with access doors
- Molded float (purple) filled with 2-lb density closed cell expanding foam (600-lbs buoyancy per module)
- Molded silo (orange) that is perforated to allow water influx and molded feet to support the system in low tide and during assembly
- Basket modules have a molded basket (turquoise) with a mesh bottom to allow upwelling, while the pump module contains a pump
- The water upwells through the mesh bottom of the basket into the basket module.
- Water is then drawn down through the central pipe.
- It moves through the pipe to the pump module.
- It is then expelled back into the ocean.
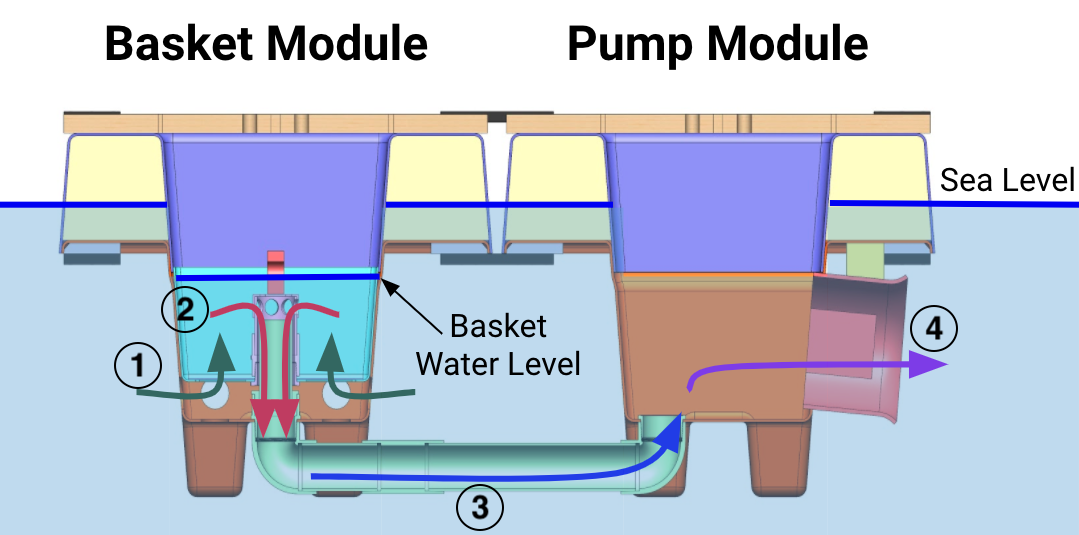
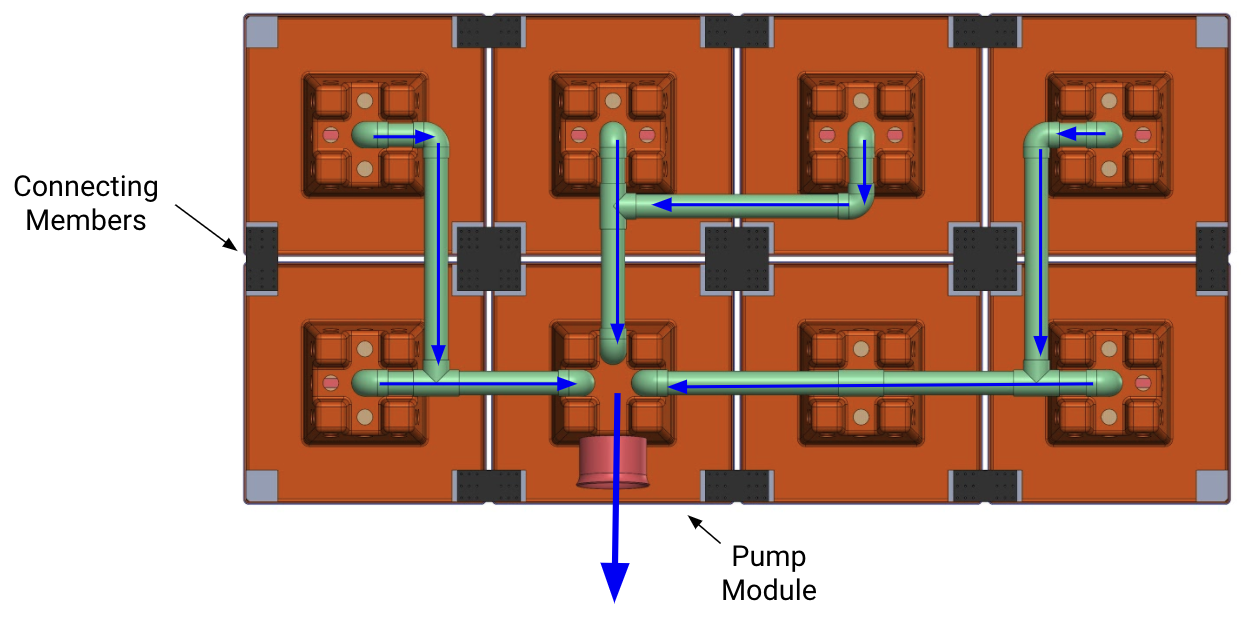
- All the parts have been designed to be thermoformed, which will greatly reduce the labor associated with fiberglass manufacturing.
- To replace the bulky rotomolded polypropylene float tanks, we used foam that takes up volume within the platform.
- The previously large central trough is replaced with one module that is dedicated for water outflow.
- The modularity of the system allows customers to choose any size and configuration they want. Furthermore, each module can be stacked on each other to reduce the device's footprint during shipping.
Floating Tumbler System
We also tested a new tumbling method of cultivating oysters. Currently, water is upwelled through the oysters, whereas our tumbling system will gently rotate and tumble the oyster seed, thereby introducing new water to the oysters.
This proposed method also reduces the need for manual sorting and cleaning, as the tumbling action will break the beaks off of the oysters. With this method, we estimate that 1 hour of labor per week will be required (as opposed to the usual 15 hours).
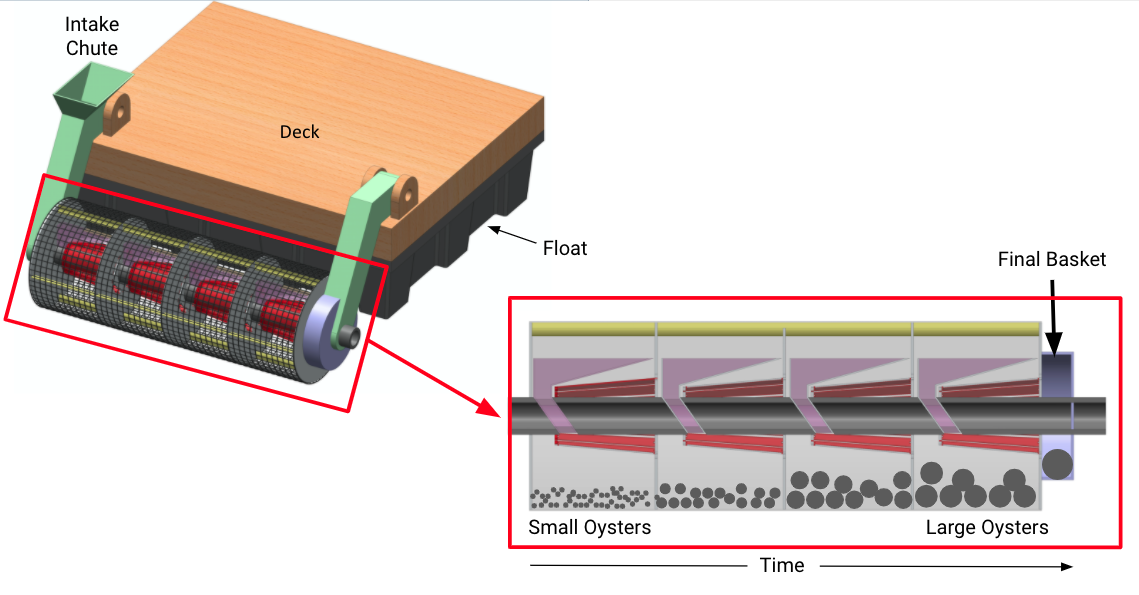
- Young oysters are placed in the intake chute, after which they enter the first section of the tumbler.
- Scoops within each rotating section pick up the oysters and drop them into a central chute.
- The oysters fall into a sorting drum. Small oysters pass through the sorting drum back into the same rotating section, while larger oysters do not pass through the sorting drum and instead travel into the adjacent rotating section.
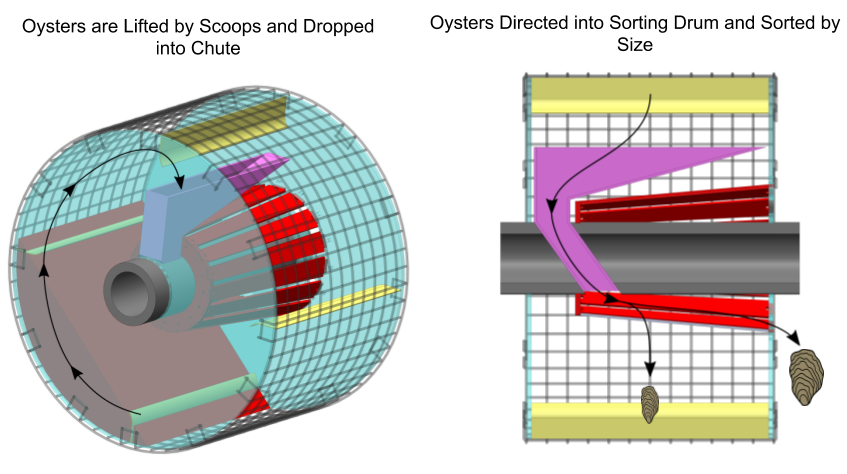
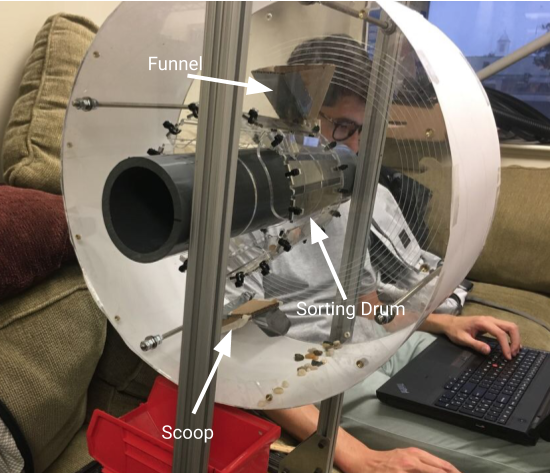
As this tumbling method of growing oysters has never been proven to work, we conducted a feasibility study to understand if tumbling oysters can effectively cultivate them.
In the experiment, we compared a miniature version of the current floating upweller system (mini-FLUPSY) to our tumbler prototype. We controlled the initial oyster mass and tested each prototype in the same body of water to expose them to the same temperature and amount of food.
The mini-FLUPSY has a flow-rate that was scaled proportionally by the mesh area. This ensures that the same flow rate of water is upwelled in the mini-FLUPSY as in the current FLUPSY. The average oyster bed depth in the mini-FLUPSY was also kept the same as in the original device.
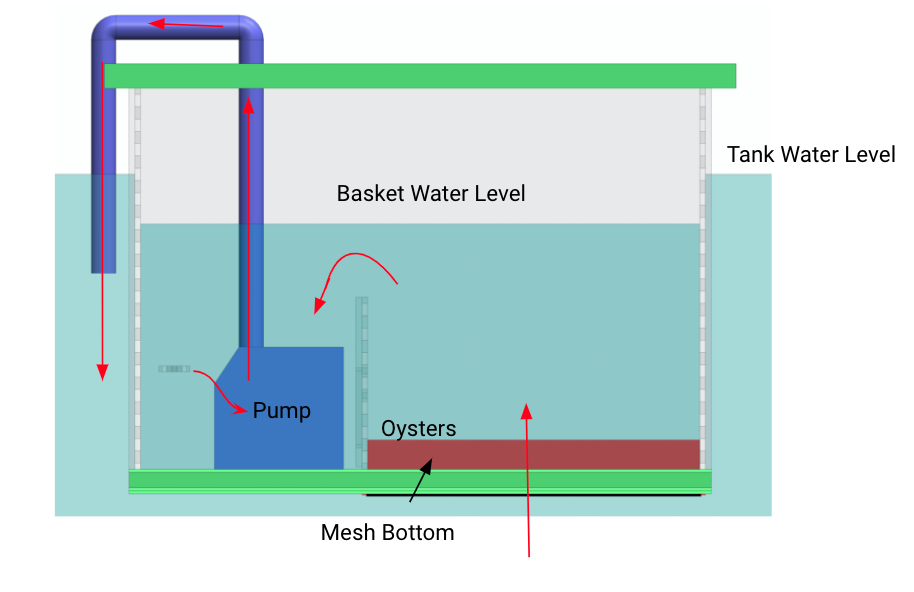
Our tumbler prototype consists of a rotating acrylic drum enclosed by both fine and structural mesh. A DC motor rotates the tumbler at approximately 1.5 RPM and was kept out of the water with a frame and belt system.
The acrylic sides have etched lines to easily track the volume increase of the oysters overtime. We did not test the sorting prototype here as we wanted to isolate the tumbling action to understand if it was a viable means of cultivating oyster seed.
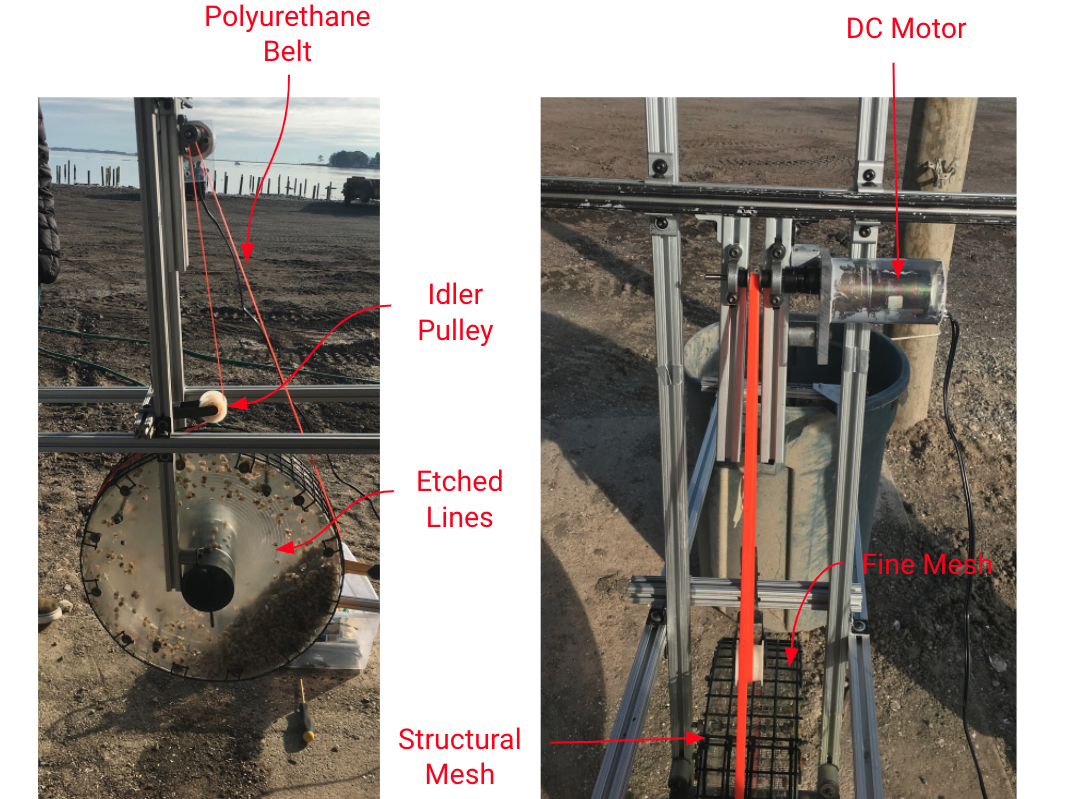
Each prototype was filled with 2.88lbs of 6mm oyster seed and placed in the same 10’ x 5’ fiberglass tank. Salt water infused with concentrated algae provided the oysters with food. Algae was consistently added to the tank to ensure the oysters were overfed (to prevent any limiting factors). Two aquarium heaters were used to raise the temperature of the water and a pump circulated the water around the tank.
Temperature was recorded hourly using a temperature logger and pictures of both prototypes were taken weekly, allowing the use of the graduations on the prototypes to estimate growth. At the end of the experiment, the oysters were weighed to see any growth.
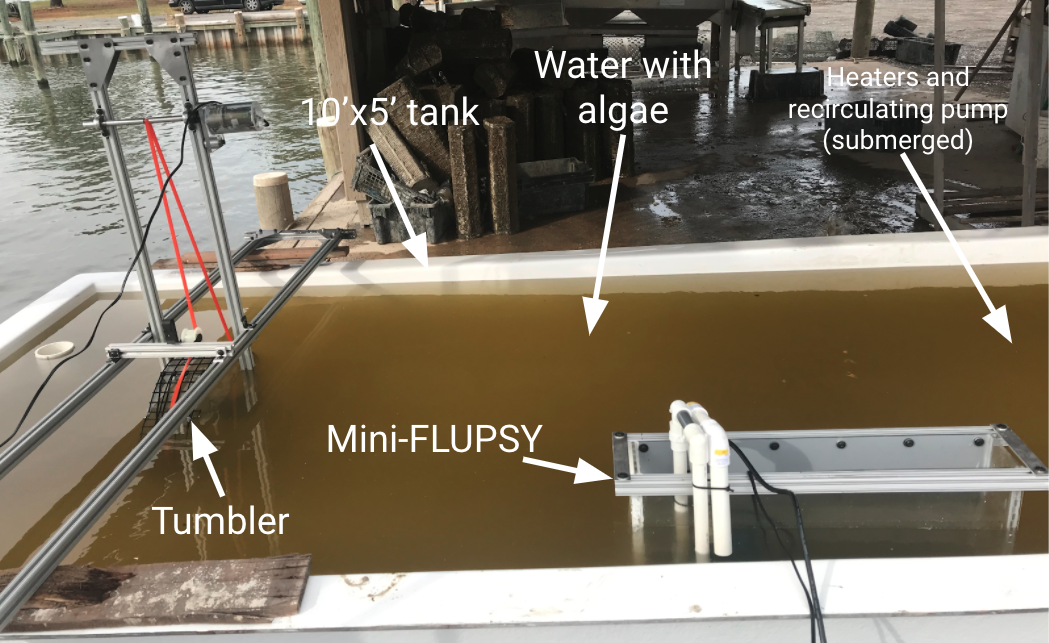
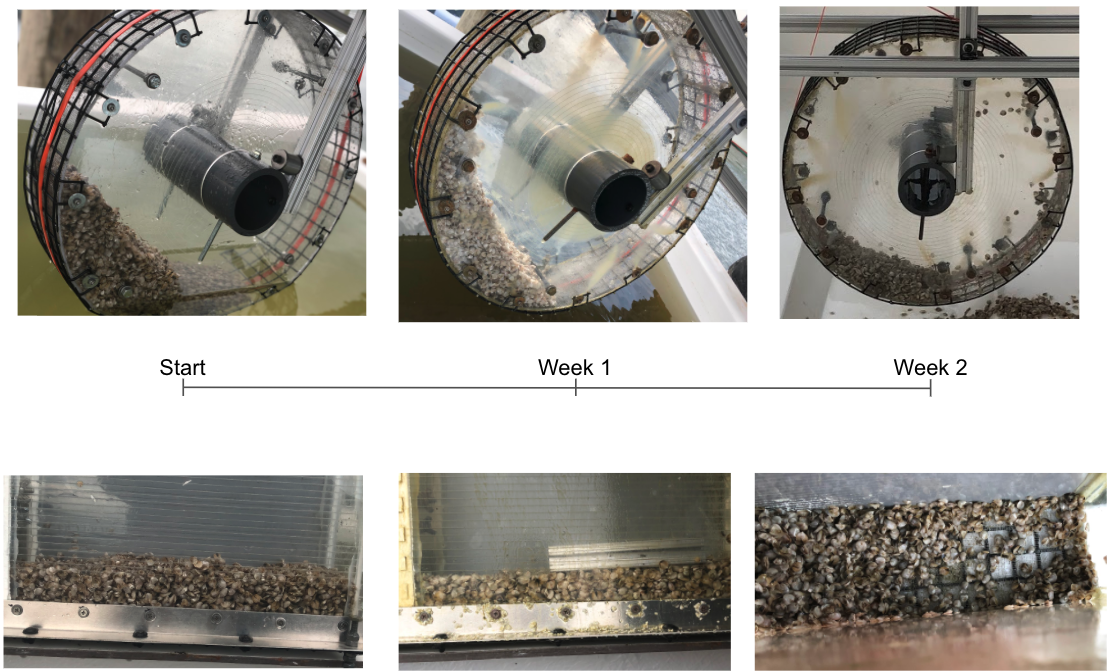
A higher mortality rate was observed in the tumbler. Possible future changes could be decreasing the RPM to make the tumbling environment less severe and including a pump that specifically introduces new water to the oysters to make up for this slower RPM and consequent water introduction.
However, our project timeline required a decision to be made. We decided to continue along the path of the new Modular Floating Upweller System, as the principle behind its operation has been proven already.
Modular Floating Upweller System - Proof of Concept
We created a proof of concept to test the functionality and usability of our new thermoformed modular system. It included one basket module, one basket, and one pump module (which has a 4000 GPH bilge pump). All components were constructed out of plywood and coated in epoxy to be made waterproof.
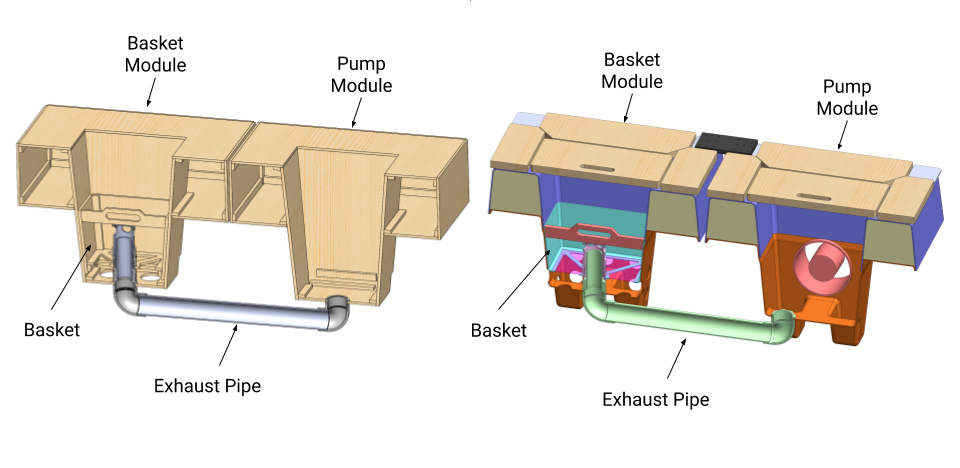
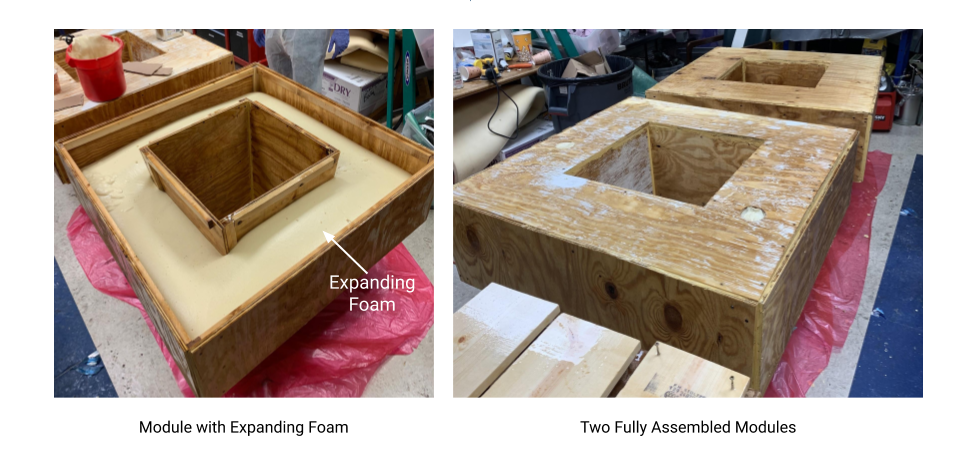
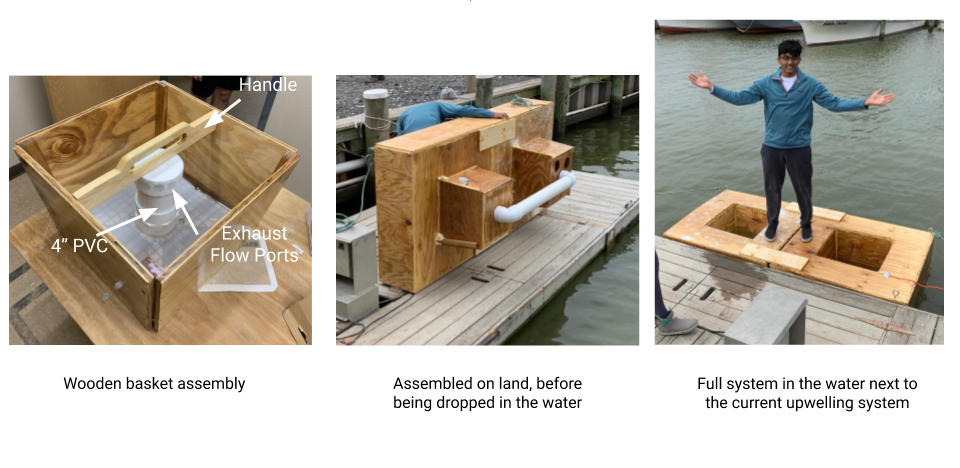
The geometries of our new design proved to grow oysters as well as the current design. Both the control sample and experimental sample weighed the same at the end of the 21-day test. Our colleagues at Hoopers Island also mentioned that the device was ergonomic and had a commendable ease of use.
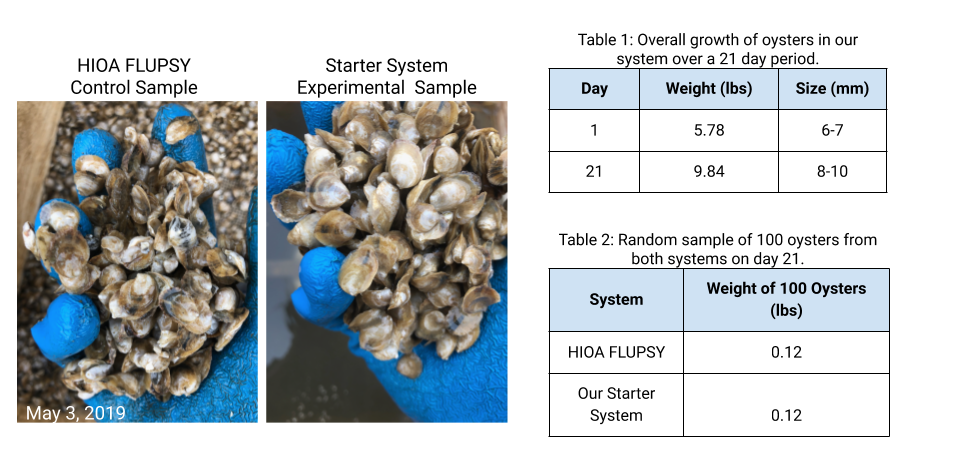
A complete 8 module system can be packed and shipped on two standard shipping pallets. All components are accounted for and have been included.
- Estimated Shipping Cost (Hoopers Island to California)
- Current FLUPSY: ~$1,700
- Modular Thermoformed FLUPSY: ~$990
- Production Costs (Materials + Labor)
- Current FLUPSY: ~$5,130
- Modular Fiberglass FLUPSY: ~$4,970 (97% of original cost)
- Modular Thermoformed FLUPSY: ~$4,176 (81% of original cost)
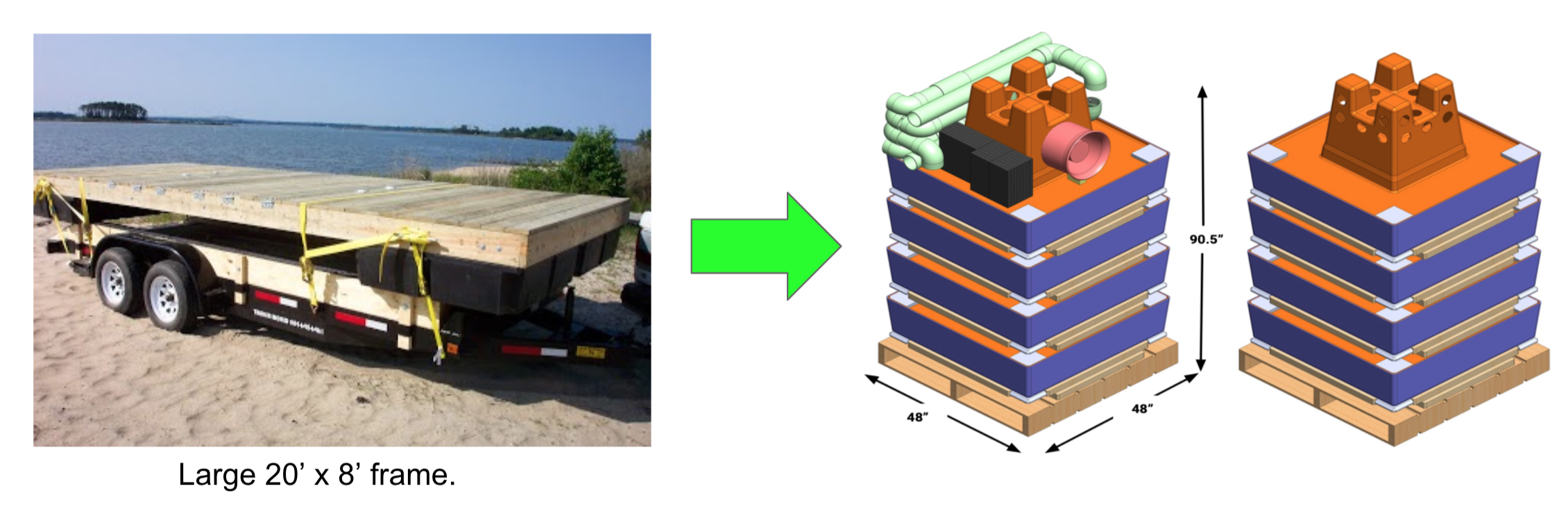
- https://hoopersisland.com/
- https://www.elementseafood.com/the-life-cycle-of-oysters-in-aquaculture/